With the increasing production of automobiles, the disposal of the used and waste tires has become the main concern to protect the environment and waste clearance. The used tires will be no longer used and it is a challenging task to maintain the waste, as they are produced in large volumes and cannot be degraded naturally. In order to overcome this problem, techniques such as devulcanization and pyrolysis are used to recycle waste tires. These techniques not only help in degrading the waste and used tires but also generate useful end products from them, which can be used in several applications and in generating profits.
Pyrolysis
Pyrolysis is a process in which the waste shredded tires or the whole tires are heated in a waste tire recycling machine which is oxygen-free. The softened rubber is broken down into small molecules and is then vaporized. This vapor exits from the reactor and can be used in producing fuel oils or can be directly used as fuel. The remaining mineral wastes are removed as ashes and are further processed to make them into useful material.
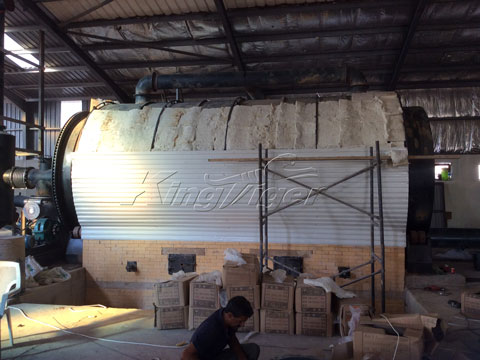
Pyrolysis Process
Step 1:
Shredding or Pre-treatment
The waste tires are cut into small pieces by the shredder. If the tires have a diameter more than 1200mm, the steel wire which is present in the side wall of the tire is pulled out and cut into bulks. If the size is less than that, this step can be avoided. These tire bulks are then crushed or shredded in the shredder. The shredder can cut the tires into 50*50mm size blocks.
Step 2:
After shredding, feed the tire pieces into the pyrolysis reactor with the help of screw conveyor, which is sealed. The burning room in the reactor uses fuels such as natural gas, diesel, or LPG to start the burning process.
Step 3:
The burning process produces hot air flow, which helps in increasing the temperature in the reactor. When the temperature reaches a certain degree, the tires are liquidified and generates oil gas. This oil gas enters the manifold, where it turns into heavy oil and drops into the oil tank. The light oil produced rises up and is directed into the condenser by damping tank, which controls the sped of the oil gas.
Step 4:
In the condenser, the oil gas is liquified into the oil. The combustible gas in the hydro seal is desulfurated and recycled to produce heat, which can be used by the reactor and saves fuel required for the process.
Step 5:
In the heat exchange system, the air that enters it through the out pipe is heated by the smoke which enters it through an inner pipe from the reactor. It is then sent into a burning room to provide oxygen.
Step 6:
The smoke is cooled in the fuel condenser and enters the dedusting chamber. The four filters in the spraying tower clean the smoke. The four filters include:
- Water wash
- Water spray
- Ceramic ring absorption
- Activated Carbon Absorption
These filters make the smoke emission meet environmental protection standards.
Step 7:
The auto screw discharger discharges the carbon black. The magnetic separator separates the carbon black and steel wire and then transports them into a storage tank.
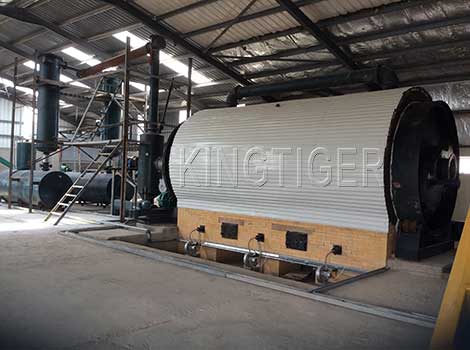
Factors that affect the cost of pyrolysis plant
1. Raw materials: It will be easy and cost effective if the plant is set up near the tires.
2. Area: Depending on the size of the plant, the area required for its establishment changes. A basic used tyre pyrolysis plant requires 400square meters area.
3. Fuel: Pyrolysis generates fuel oil and gas which can be used in keeping the machine running. Hence a very less amount of fuel is required to initiate the process.
4. Power: It uses about 100KWH power per day.
5. Labor: It requires minimum labor, as low as 3 persons, as the entire process is automatic and there are very few stages where labor is actually required.
6. Maintenance: The pyrolysis plant doesn’t emit so much of waste and has a very less maintenance cost if it is purchased from a quality producer. The only maintenance required will be regular cleaning of the machine and per month, it hardly costs around 100USD.
Choosing the right capacity pyrolysis plant depending on the size of the business and the quality of the machinery can maximize the profits for customers: www.kingtigergroup.com.